REALISE CCUS Project Final Event
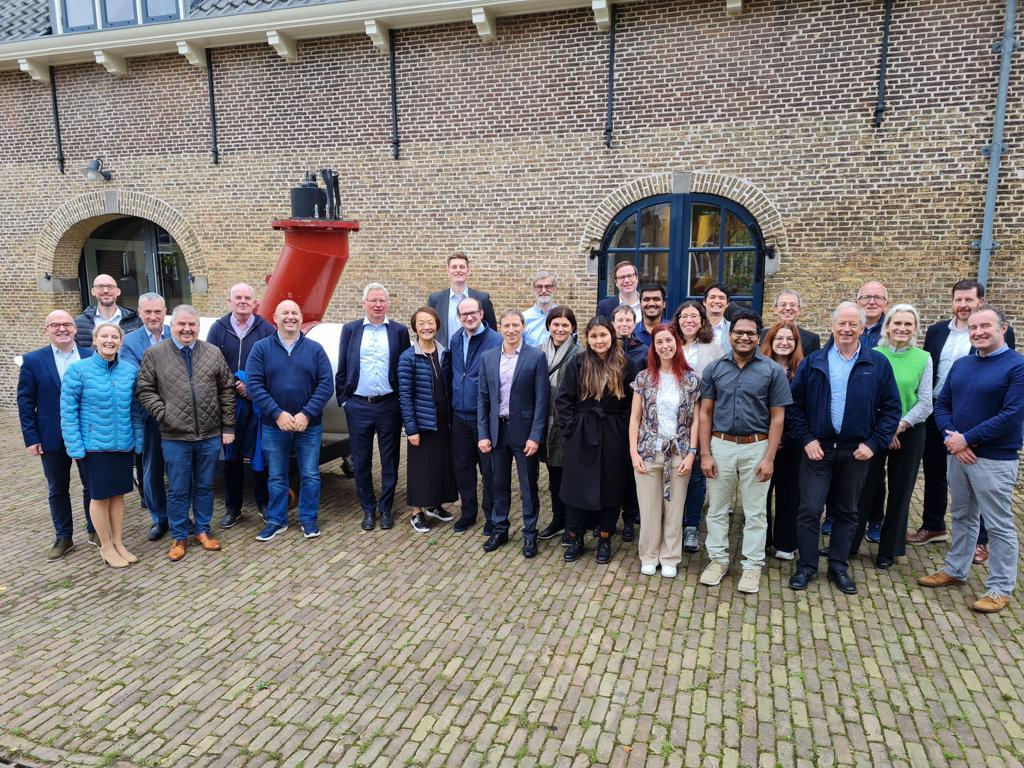
The final project meeting was hosted by TNO at Buccaneer Delft, The Netherlands, on the 24-25th October.
Over 30 project partners gathered in person to discuss their achievements since the project started in May 2020 and future areas of work to support CCUS delivery in the refinery sector. They were joined by online participants, including industry experts and scientists from across Europe, China and South Korea.
Through a series of talks and panel discussions, attendees learnt about the carbon-capture demonstration campaigns performed by REALISE partners, ways to reduce the cost of carbon capture, the importance of effective public engagement and of tackling political and regulatory barriers to CCUS deployment.
Following the opening remarks by Peter van Os, Senior Project Manager at TNO, and Inna Kim, REALISE CCUS project coordinator based at SINTEF, Hanna Knuutila (NTNU) and Filippo Bisotti (SINTEF) gave an overview of the results from work package (WP) 1: optimising and validating technologies for refineries.
Over the course of the project, WP1 has characterised the low-energy solvent HS-3 and developed strategies to optimise its use, as well as performed long-term tests of plastics to validate their potential for use instead of metals in the absorber and desorber columns of CO2 capture plants. The data obtained from this work package were used in the development of process simulation tools and for Techno-Economic Analysis (TEA) of three business cases.
Next, Eirini Skylogianni (TNO) and Thor Mejdell (SINTEF) summarised the results of the carbon-capture demonstration campaigns using HS-3 solvent at the Irving Oil Whitegate Refinery in Cork, Ireland, and the CO2 pilot plant at Tiller, Norway (WP2).
TNO’s miniplant, which was made ATEX complaint to enable testing on-site oil-refineries, has a 25 kg CO2/day capture capacity and can operate 24/7 while being controlled remotely. It was installed at Irving Oil and captured CO2 from flue gases from six stacks with CO2 concentrations ranging from 5.5-8.2 vol %. The miniplant was in operation for 3000 hours.
The campaign at Tiller (2000 operation hours) further demonstrated the consistent high capture rates and low energy requirements (3.1 MJ/kg CO2 for 11 mol % CO2) of the HS-3 solvent, and measured impurities in the liquefied CO2 product using a CO2 Compressor and Liquefaction Unit (CCLU) commissioned and built as part of the REALISE CCUS project. Measuring the impurities in captured CO2 is important for assessing and de-risking CO2-transport and CCU applications.
Next, Des McCabe (Ervia) and Ragnhild Skagestad (SINTEF) presented results from WP3 on carbon capture integration and full CCUS chain assessment based on the Cork cluster, which comprises two gas-fired combined cycle power plants and Irving Oil refinery located close to an offshore gas pipeline connected to a depleted gas field.
A comparison of ways in which CO2 capture could be configured in the cluster highlighted the advantages of building a single integrated facility, treating both the refinery flue gas and the power plant flue gas. Their cost-benefit analysis indicated that indigenous storage at Kinsale Head gas field is a more economical option than exporting the CO2 for storage in Norway.
When looking at the socio-political barriers to CCS, public resistance, policy uncertainty and lack of regulation and infrastructure were found to be the most important. Governments also have a critical role in establishing the policies and regulations to create a business case for private sector investment in CCUS technology.
Søren Jensen (Pentair) presented a TEA for carbon capture at Irving Oil refinery using data generated in the project. The estimated cost per million tonne of captured CO2 ranges between 78-92 Euro depending on the solvent that is used (MEA or HS-3) and on whether steam is generated on site or not.
In the afternoon, Jasper Ros (TNO) led a workshop on the CO₂ capture tool developed by TNO called OCTOPUS (Online Calculator To Optimize CO2 capture Processes for mUltiple Stacks; short introduction can be found here), and Romain Viguier (SCCS) moderated a REALISE Industry Club panel discussion. A panel with representatives from Bord Gáis Energy, Cybernetica, Equinor, Pentair, Irving Oil, TNO and ESB discussed the current and future implementation of CCUS in existing refinery plants.
By evaluating, testing and advancing REALISE’s innovative CCUS technologies, the Industry Club has helped understand the industrial context of CCUS development. Members of the Industry Club have demonstrated throughout the project their readiness to engage in partnerships, share best practices, and collaborate closely with research institutes. This culture of collaboration holds great promise for addressing the environmental challenges we are facing and reducing the development costs associated with CCUS implementation.
On day 2, CCUS business cases for refineries in China and South Korea were presented by Guojie Qi (Tsinghua University) and Jiyeon Lim (SK Innovation), who have been working with Davide Bonalumi (Politecnico di Milano) and Abhishek Subramani (TNO), respectively.
Xi provided an overview of current CCUS projects in China’s energy and refinery sector before focussing on the Jinzhou Refinery case study. In collaboration with REALISE project partners, Xi has characterised the refinery’s flue gas, developed simulation models and performed a TEA that compares the use of HS-3 to 30 wt % MEA. The findings have prompted further work into the use of advanced solvents to improve capture performance and ways to optimise the utilisation of waste heat to reduce the cost of retrofitting CO₂ capture to the refinery.
Lim and Subramani outlined the status of CCUS in South Korea and their work on the SK Ulsan Complex, Korea’s oldest refinery. They analysed the flue gases of three stacks, considered four integration options and modelled MEA and HS-3- based capture processes using the OCTOPUS database. They found that steam price is a major cost driver for MEA, and for HS-3, it is also the cost of solvent. In future studies they will consider solvent management technologies to improve the economic feasibility of carbon capture.
The business case presentations were followed by a summary of the work carried out on the societal, socio-political and commercial context for CCS deployment by Niall Dunphy (University College Cork) (WP4). Over the course of the REALISE CCUS project, Dunphy and colleagues have carried out a critical review of selected education and public engagement (EPE) programmes from around the world, developed and tested their own EPE programme and considered ways to de-risk and incentivise CCS projects.
In a report assessing societal readiness, Dunphy and Breffni Lennon (University College Cork) propose policy recommendations and regulatory changes to address some of the barriers to CCS implementation such as public scepticism, technical expertise shortage, policy lacunae, as well as uncertainties around cost and demand. Their recommendations to national governments include: providing public information campaigns on the potential of CCUS technologies to mitigate climate change; developing detailed decarbonisation roadmaps that explain the role of CCS in phasing out of fossil fuels; partnering with other countries to create and share CCS-related infrastructure; and, undertaking a regulatory audit to identify and characterise shortcomings in legal and regulatory frameworks necessary for CCS.
In a second REALISE Industry Club panel discussion, moderated by Dunphy, representatives from SCCS, TNO, Concawe, SINTEF and BGE further discussed the socio-political aspects of CCUS implementation in plants, including refineries. Being able to effectively communicate the 'why?' of large infrastructure projects is one of the key aspects for successful societal engagement. In the case of CCUS, this is being able to: produce low-carbon products that the world will still need for some time to come; decarbonise hard-to-abate industrial processes, such as cement, steel and chemicals; and reduce the excess atmospheric CO2 that has been accumulating since the start of the Industrial Revolution.
The event ended with a partners' meeting in which the project milestones, plan for exploitation and management of the project’s legacy were agreed.